5 steps to perfect concrete patching with HB70
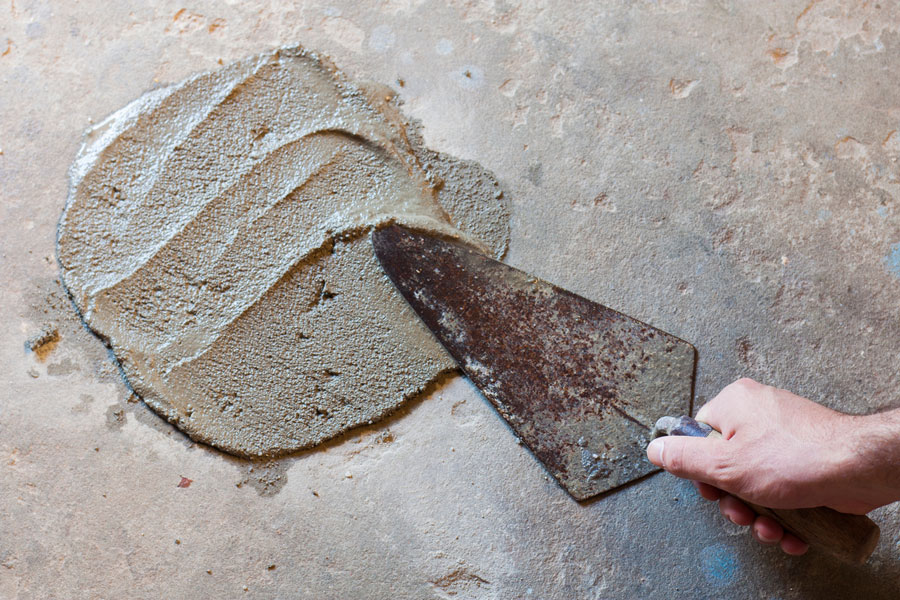
High build mortar is a type of filler frequently used when patch repairs need to be made to damaged concrete. Repair mortars need to tick a lot of boxes – they need to be durable, easy to apply, not crack or shrink, not damage reo or other nearby steel structures, be watertight, and resist chemical damage. They also need to mix evenly when added to water, so that the mortar goes on smoothly.
This is a lot to ask of a simple dry powder, however, many manufacturers invest in extensive R&D programs to create products that meet these criteria. No matter how good the dry mix is, however, proper preparation and application is the key to getting the perfect result.
Using the right mortar combined with the ideal mixing and application procedure is crucial for the success of any concrete repair job. High build mortars such as Fosroc Renderoc HB70 and similar HB mortars are supplied as dry powder blends which require a specified volume of water to be added on-site. This produces a highly consistent, high strength repair mortar.
Renderoc HB70 is polymer modified which means it offers both good handling characteristics and minimal water demand. When cured, Renderoc HB70 has excellent compatibility with concrete and is great at repelling water. Manufactured for vertical and overhead work, its high build formula can be trowelled or sprayed on depending on your needs.
Fosroc Renderoc HB70 Technical Application Guide
Whichever mortar you are using, it is crucial to follow the manufacturer’s guidelines when it comes to priming, adding water and applying the high build mortar. Make sure you consult the full technical data sheet before you start.
To give you an outline of the process, here’s a quick guide on how to get the best results using Fosroc Renderoc HB70.
Renderoc HB70 Basics
- Prep
Cut back the edges of the area to be patched to at least 5mm to provide a square edge. Clean the surface and remove any dust, flaking material, oil or grease. Expose any corroded steel in the repair area using a process like grit-blasting. Exposed steel needs special attention.
- Prime
The existing concrete should be saturated with any residual surface water removed immediately prior to applying Renderoc. Under severe drying conditions or on hot days, repeated soaking may be necessary to ensure the substrate is still saturated at the time of application. Primers such as Nitobond HAR can be used to improve the build thickness, and special bonding agents should be used if the concrete is likely to remain damp permanently.
- Add water
If you add too much water, it could weaken the mortar and lead to higher levels of shrinkage. Using the right mortar and mixing technique is crucial. Make sure you add the powder to water, not the other way around. With 2.8 - 3 litres of fresh, clean water in a tub, add half the 20kg bag and mix for 30 seconds, then slowly add the remaining powder, continuing to mix it for 3 or 4 minutes. Mix at a slow speed using a specialised mixing paddle attachment. The maximum water ratio should be 3 litres to a 20 kg bag, but this may be slightly less depending on the ambient temperature and the consistency required. Mixing part bags is not recommended.
- Application
Renderoc HB70 has been specifically engineered for vertical and overhead repair work. It can be applied in sections up to 100 mm thickness on walls (80 mm in overhead locations) in one go, without having to use formwork. Its build can be increased by wet spraying (up to 150 mm vertically and up to 100 mm overhead). Of course, this depends on the condition of the existing concrete and steel reinforcement. HB70 should not be applied at less than 5 mm thickness. The mortar can be applied with a trowel or sprayed. Remember to clean up tools, equipment and mixers with water straight away as cured mortar will set solid.
- Curing & Finishing
Renderoc HB70 should be cured immediately after finishing with a product such as Nitobond AR or Concure A99. It’s recommended that the curing compound be sprayed on to the surface of the finished Renderoc in a continuous coat. Additionally, over coating with finishing coats such as clear sealants can extend the life of your repair job by offering additional protection against rain and harsh weather.
About Fosroc Renderoc HB70
Renderoc HB70 is supplied as a ready to use blend of dry powders which requires only the addition of clean water to produce a highly consistent, high strength repair mortar.
The material is based on the latest advances in cement, fillers and chemical additives technology and is polymer modified to provide a mortar with good handling characteristics while minimising water demand. The hardened product exhibits excellent thermal compatibility with concrete and outstanding water repellent properties. The low water requirement ensures fast strength gain and long term durability.
Renderoc HB70 is alkaline and will protect steel reinforcement. It is specifically designed for locations where high build and high compressive strengths are required or in locations where good abrasion resistance is necessary.
Technical specs
- Renderoc HB70 one component polymer modified high build cementitious mortar
- Conforms to the requirements of BS EN 1504-3 Class R4
- Compressive strength of 70MPa at 56 days
- Drying shrinkage of <400 microstrain at 7 days
- Drying shrinkage of <600 microstrain at 28 days
- Flexural Strength >7 MPa
- Indirect Tensile Strength >5 MPa
Advantages
- High strength, high build and high abrasion resistance
- High-build formula reduces the need for formwork or multiple coats, thereby saving time and money
- Low carbon foot print thanks to a formulation based on supplementary cementitious materials. Contains no chloride admixtures.
- Can wet spray applied for fast, exceptionally high-build repairs with enhanced strength
- Very low permeability provides protection against carbon dioxide and chlorides
- Excellent bond to SSD (saturated surface dry) concrete substrates – no separate primer required in most circumstances
- Shrinkage compensated