Glove Standards in Australia
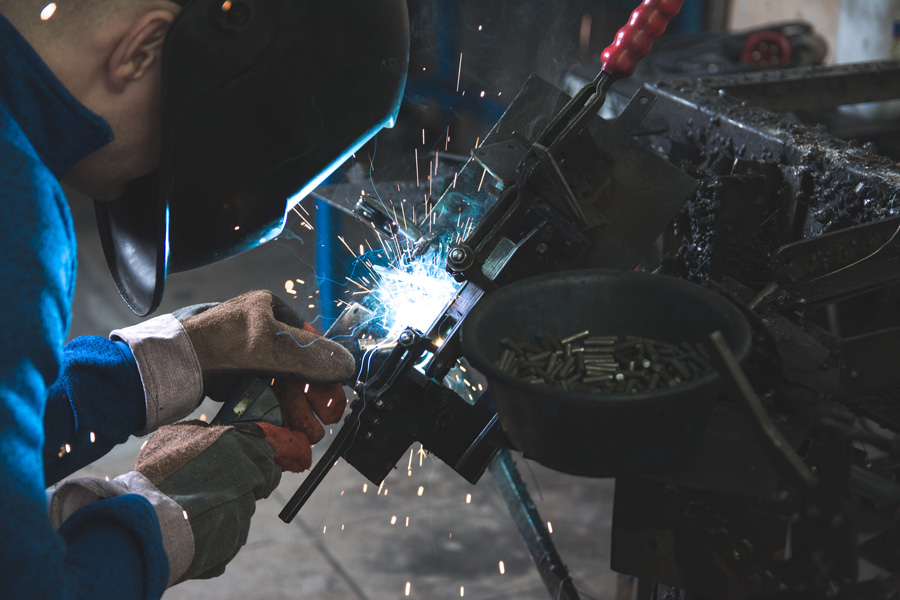
Decoding European and Australian Standards for protective gloves, and how to identify the right gloves for your workplace
Gloves are an essential piece of equipment on almost any work site. From protecting against abrasions and cuts, to shielding workers from chemical risks, to reducing the risk of puncture injuries, gloves provide a wide range of protection.
Specialist gloves for welding, vibration protection and high voltage gloves for electrical work can be critical to the safety of workers in these industries. This article looks at the different types of workplace hazards, and the extensive list of international and Australian standards for protective gloves.
Standards approved hand protection is mandatory across a range of work environments, but how do you know which gloves to choose?
First up: risk assessment
To ensure your hands are adequately protected at work, firstly you should conduct a risk assessment. A risk assessment will ensure you’re aware of the different types of hazards that exist in the workplace.
Ultimately, PPE such as hand protection should be the last line of defence. Further to this, workers should only wear hand protection if you cannot engineer out the hazard or change the work process. This logic follows the widely accepted heirarchy of workplace hazard controls.
If you are unsure about the hazards at your worksite, you should certainly get in touch with your workplace health and safety officer or an OH&S professional.
Finally, once you have completed a risk assessment, you may find some scenarios where you need to use hand protection.
Types of hazards
Depending on your workplace, there are a wide variety of hazards that workers could potentially be exposed to.
The most common are abrasions, cuts, punctures and chemicals. Certain industries such as medical or waste disposal may also identify needle stick and biological hazards. On the other hand, workers who engage in high voltage electrical work need protection from electric shock. Likewise, workers who are welding and brazing need protection from radiant heat.
Let’s look at some common work processes and the typical hazards involved.
ABRASION
Abrasions can be caused by construction work, steel fabrication, demolition, mining and quarry work, brick or block handling, and landscaping work.
CUTS
Hands are easily cut by sharp sheet metal, during salvage work, working with scrap metal and mechanical processes using knives or blades.
CHEMICALS
Chemicals can damage skin during work such as cleaning, degreasing, solvent handling, using acids, painting and handling fuels.
PUNCTURES
Puncture wounds are different to abrasions and can be caused by wire handling, handling steel mesh, swarf, as well as waste handling.
RADIANT HEAT
Radiant heat and burns can be caused by welding processes, brazing, and working with molten substances such as asphalt.
BIOLOGICAL
Biological hazards exist in medical and first aid situations, but also in cleaning and waste handling and in certain food processing work.
NEEDLE STICK
Needle puncture injuries can occur in cleaning and medical work, and also occur in waste related work or some landscaping operations.
ELECTRIC SHOCK
Obviously, electrical work carried out in the vicinity of live wires carries the risk of high voltage electrical shock.
Australian Standards for Protective Gloves
The Australian and New Zealand Standard AS/NZS2161 is the overall standard for occupational protective gloves. These local standards mirror the European standards EN407, EN420, EN374, EN388 and EN511, although some differences do exist.
The Australian Standards for protective gloves gives guidance on selection, use, maintenance and hygiene when it comes to gloves. Workers and supervisors should follow these guidelines for appropriate glove selection for the task at hand. Additionally, maintenance and disposal of gloves is paramount to maintain a healthy work environment. The standard gives advice on decontamination, cleaning and storage of gloves. This ensures that the optimum glove performance is maintained.
It's worth noting that on the manufacturer's side, this Australian Standard does not give requirements for performance and testing. These are covered off in separate standards.
Do I really need Standards-approved gloves?
The gold standard International PPE directive 89/686/EEC indicates that in some cases, Standards Approval is not necessary. Therefore, in these ‘low risk’ cases such as gloves used for basic cleaning and tidying, manufacturers don’t need independent certification.
However in most workplace scenarios, gloves are designed for situations which fall into either intermediate or irreversible risk. It is these risks which dictate that a Standards Approved glove must be used.
To illustrate further, ‘intermediate risk’ covers every day work site hazards such as abrasions, punctures and cuts. These must be tested and certified.
‘Irreversible risk’ relates to gloves designed to protect against chemicals and other hazards that can cause serious injuries. These must be tested and certified. Additionally, the manufacturer must be able to guarantee the quality and consistency of manufacturing, for example with an ISO certification or similar.
So – considering most civil, construction, building and demolition workers who may be reading this are likely to be exposed to intermediate or irreversible risks, let’s explore the standards further!
International Standards
As Australia and New Zealand have largely adopted the international glove standards and categorisation, we’ll look deeper into what these European standards mandate. Australian Standards for protective gloves incorporate most of these guidelines.
EN420: GENERAL OCCUPATIONAL PROTECTIVE STANDARDS
This standard covers minimum performance levels such as the length a glove must be for each hand size, the level of dexterity available, the composition, and manufacturer markings. Additionally, EN420 states how gloves should be packed, stored, cleaned and maintained.
Certain requirements need to be marked clearly on the glove. To illustrate, the glass gripper glove shown here shows the requisite information:
- The CE mark
- The size
- The standard to which it is approved (in this case mechanical)
- A number allowing its manufacturing and certification origins to be traced
Decoding EN Standards
ONE OF THE MOST COMMON RISKS: ABRASIONS AND CUTS
The European Standards cover a range of hazards and each standard has different testing methods depending on the type of glove. One of the most common hazards in our industry is abrasions and cuts from day to day tasks in civil construction or demolition work. These are known as ‘mechanical’ risks.
European standard EN388 covers 4 types of mechanical risks, namely as abrasions, cuts, tears and punctures. Gloves are tested for resistance against these four risks and subsequently given a rating for each one. The ratings range from 1 for low performance through to 5 for maximum performance. These numbers are generally displayed as 4 digits that appear under the shield-shaped pictogram featuring a hammer, indicating mechanical risk protection.
For example, this UVEX Unilite glove rates very well for abrasion resistance (as indicated by the ‘4’ rating), but is not the best option for cuts or punctures (indicated by the 1’s).
Below is some more detailed information on the testing methods for each type of glove.
Common standards marks
EN388: MECHANICAL RISKS
This standard tests for abrasion, cut, puncture and tearing. The rating is shown with a pictogram followed by four numbers, each representing its performance against a specific hazard. The first number indicates abrasion resistance, measuring the number of cycles required to abrade through the glove. The second number indicates blade cut resistance. The next is for tear resistance, a rating based on the force in Newtons required to tear the glove. Finally, puncture resistance is rated based on the amount of force required to pierce the glove.
EN511: PROTECTION FROM COLD
EN511 applies to any gloves that are designed to protect a workers hands cold (down to -50°C!). This includes both convective cold (such as working in a cold store environment) and contact cold. The protection level is indicated by three performance levels related to convective and contact cold, as well as water penetration.
EN374: CHEMICAL RISKS
This standard indicates how well gloves must protect workers against chemicals or microorganisms. Along with the pictogram, a three digit code is shown. Sometimes there can be additional numbers. These numbers relate to the list of 12 common chemicals such as acetone, sulfuric acid and methanol. To pass the test, the glove must withstand at least 30 minutes before the chemical breaks through the glove.
EN407: THERMAL RISKS
This standard specifies thermal performance for protective gloves against thermal risks such as radiant heat. The degree of protection is shown by a pictogram followed by a series of six performance levels, relating to specific protective qualities. These include flammability, contact heat resistance, convective heat resistance and radiant heat resistance. Additionally, the gloves are tested for resistance to small and large splashes of molten metals.
EN12477: WELDING GLOVES
Gloves for welding and hot work are broken into Type A and Type B, where type A indicates that heat protection is more important. Type B indicates that flexibility and mechanical protection is more important than heat resistance. These gloves display ratings for both the Mechanical and Thermal pictograms.
THE CE MARK
The CE mark is ultimately a seal of approval from European design directives such as the directive for PPE. It is not a standards mark itself, however, it informs the purchaser and the user of the glove that it meets essential criteria and performance standards.
Jaybro offers hand protection for common work processes
Welding gloves provide both thermal and mechanical protection. Constructed from heavy duty split leather, they have a long cuff providing lower arm protection.
High voltage electrical gloves are perfect for energy, transportation and utilities, and protect against a electrical and arc hazards. These are compliant with IEC60903 for electrical insulating gloves.
These UVEX Unidur gloves offer both a high level of sensitivity and dexterity and also high cut protection indicated by the first digit on the code.
Glass gripper gloves have a rippled latex palm that offers exceptional grip, making them ideal for handling glass, ceramics and other hand to handle items.
Confused? We can help!
The team at Jaybro are your local workplace safety experts. If you need assistance choosing the right glove for your application, give our friendly team a call on 1300 885 364, or speak directly to our Safety team for specialist advice on hand protection and other types of PPE.
A NOTE ON EN388 MECHANICAL RISK:
In the quest to protect workers as completely as possible, standards both locally and in Europe are constantly revised.
Recently some changes were implemented to the European testing methods. These have therefore resulted in slightly different ratings featuring an additional number printed on the glove. Essentially, the newer test methods aim to make up for some ambiguity in the original cut resistance test. This also harmonises the standards somewhat with US standards.
The original test used a rotating circular blade to measure cut resistance, and the newer standard uses a sliding blade instead. The glove is assigned a cut protection class on the basis of this value. This test is regarded as a more accurate guide to cut resistance.
However, until the new standard has been formally phased in, the existing four digit code remains valid. Also, although we utilise the EN 388 standard in Australia and New Zealand, these recent changes only apply within the EU at the moment. Therefore, you might notice the additional digit (4 numbers plus a P for pass) on some gloves that have been recently manufactured in Europe.
In summary: at the time of writing, gloves with either a four or five digit EN388 standards mark are equally acceptable.
Disclaimer: This article is produced as a guide only and is not a replacement for official workplace health and safety advice. Always conduct your own research and contact an occupational health and safety officer to determine the right PPE for your environment.